A large foundry had four large 200-hp air compressors that were water-cooled and were having overheating problems. The units were capable of inlet modulation control, where the inlet valve of the compressor closes off the intake to control the output flow. Use of this control mode reduces the flow output of the compressors and the power consumption, but the reduction is not linear, only a 3% reduction comes with every 10% reduction in flow. With lower power consumption, the overheating problem was reduced — allowing the compressors to run without tripping off on over-temperature, but greatly affecting system efficiency.
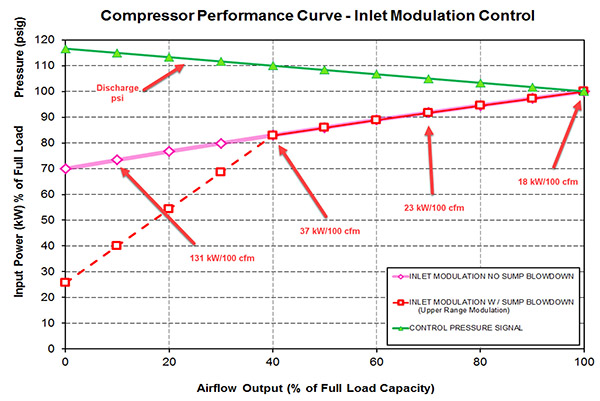
A compressed air auditor measured the compressors and found the average loading was about 50% on all four compressors; they had all been set up with identical setpoints. The auditor could see the flow output on each compressor was averaging half the rated output, but the power consumption at this 50% point was about 31 kW for every 100 cfm output. Normal specific power for a fully loaded compressor of this type, at its most efficient point of 100% flow, was supposed to be 18 kW per 100. The compressors were all consuming about 70% more power than normal when sharing the average load. And, when the loading went down to 30% flow, the compressors consumed more than 2.5 times normal power.
The compressed air auditor calculated the cost of the compressor power consumption and found that the compressors were consuming about $510,000 per year in total electrical costs! About $210,000 per year could be saved if the compressors could run in a properly controlled manner, eliminating the modulation control mode, turning off compressors unneeded compressors, and running the remaining compressors at full load. Estimated upgrades and repairs to the cooling system were about $80,000. There was money left over in the savings from the proposed project to replace one of the aging compressors with an efficient VSD controlled unit to save even more.
Load sharing lubricated screw compressors is expensive, consider other alternative and save.
Leave a Reply